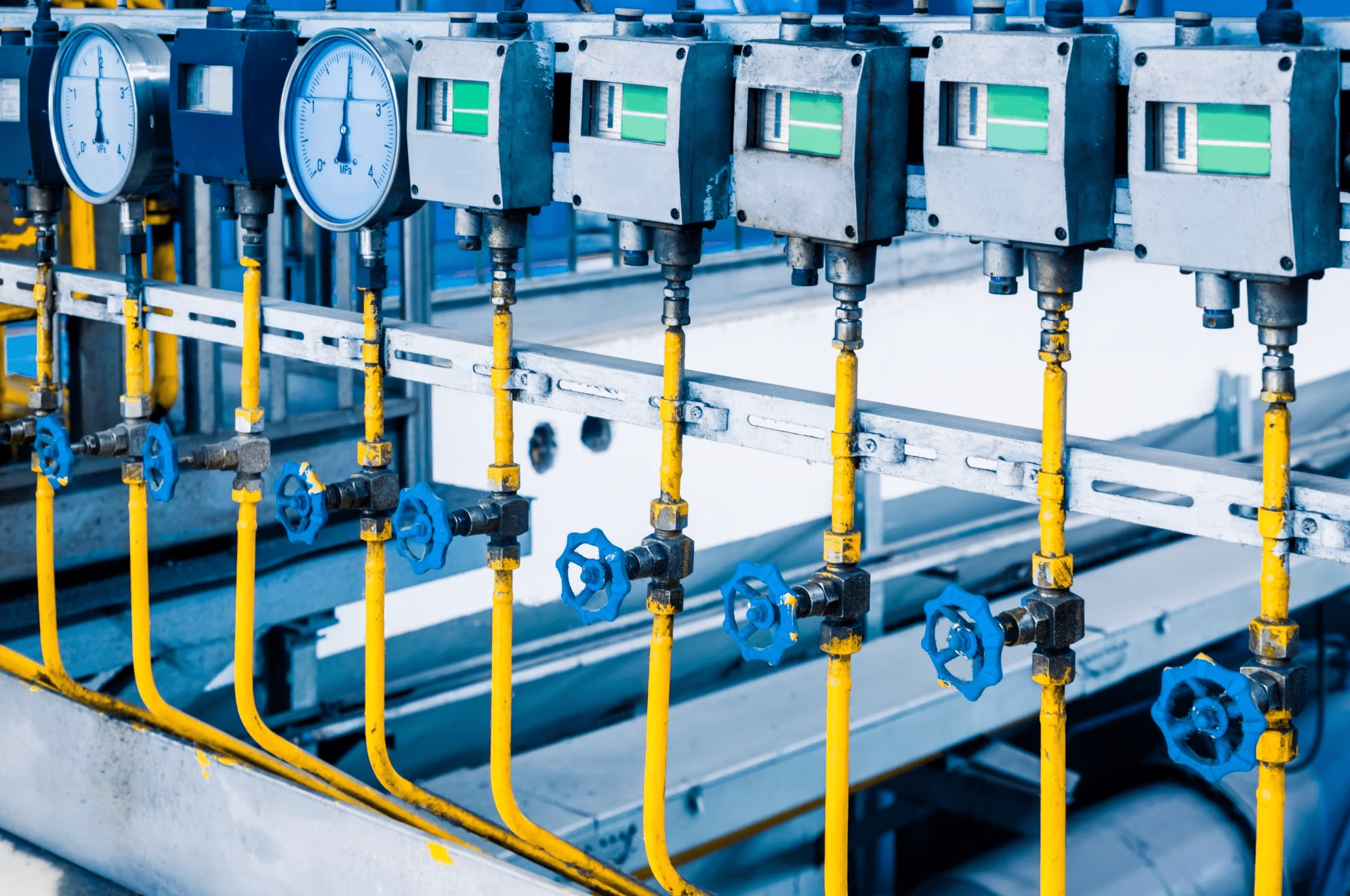
Spektrální termografie
21. 7. 2023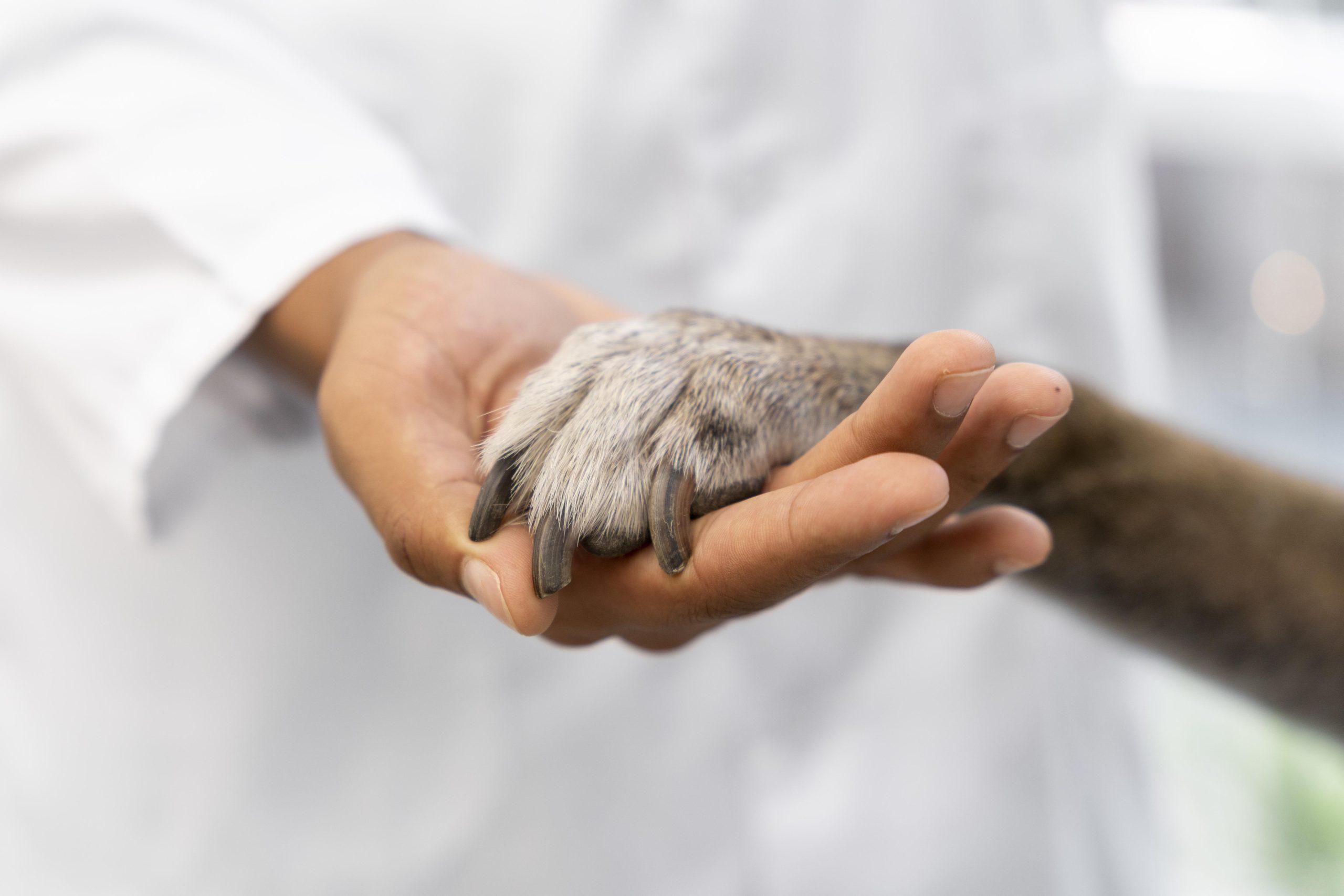
Využití termokamer ve veterinární medicíně
21. 7. 2023Využití termokamer při kontrole výroby plastikářských forem
Kvalitativní parametry vyráběných výstřiků z termoplastů a z kompozitních materiálů s termoplastickou matricí jsou značně určovány teplotními ději, které probíhají při procesu vstřikování. Tyto teplotní děje lze velmi dobře vizualizovat a pozorovat termokamerami. Výstupem z termokamery je pak termogram, který popisuje, jak se v čase mění teplotní pole formy od výchozího až po konečný stav.
Jedním z hlavních problémů, které se u výstřiků objevují, jsou deformace. Deformace jsou způsobené zejména konstrukcí výstřiků, použitým termoplastem a jeho smrštěním. Rozdílné místní hodnoty smrštění výrazně souvisejí s rozdíly teplot ve výstřiku.
Následující studie popisuje také sledování časového průběhu teplotních polí chladnoucích výstřiků a porovnání těchto teplotních polí s výsledky simulací, včetně porovnání vnější teploty a teploty uvnitř stěny výstřiku. Zde mohou být poměrně velké rozdíly s ohledem na velice špatnou tepelnou vodivost zejména kompozitních materiálů.
Úvod
Jako modelový příklad využití termokamery v plastikářském průmysl byla analyzována problematika výroby tělesa světlometu (Obr. 1) vyrobeného z vysoce teplotně odolného PA kompozitu PA6T/XT – GF 35, ZYTEL HTN 51 G35 HSL Black s obsahem 35 % krátkých skleněných vláken.
Při měření povrchových teplotních polí výstřiků bylo použito následujícího vybavení:
- Termokamera FLIR T640
- Software FLIR TOOLS+ na zpracování termogramů
- Kontaktní teploměr AHLBORN THERM 2420
- Termočlánkové čidlo Fe-Ko FT 106
- Laserový skener 3D – ROMER ABSOLUTE ARM 7320
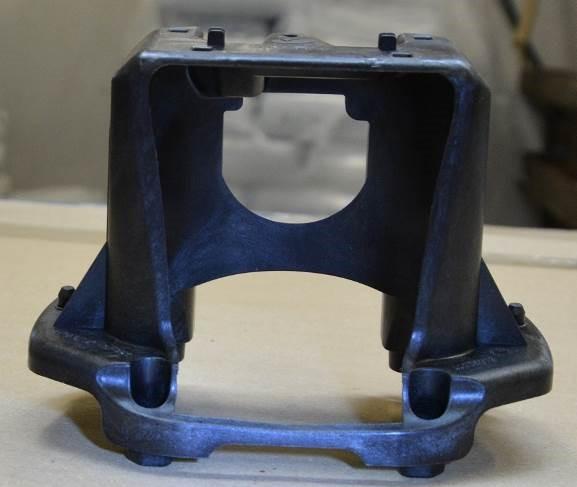
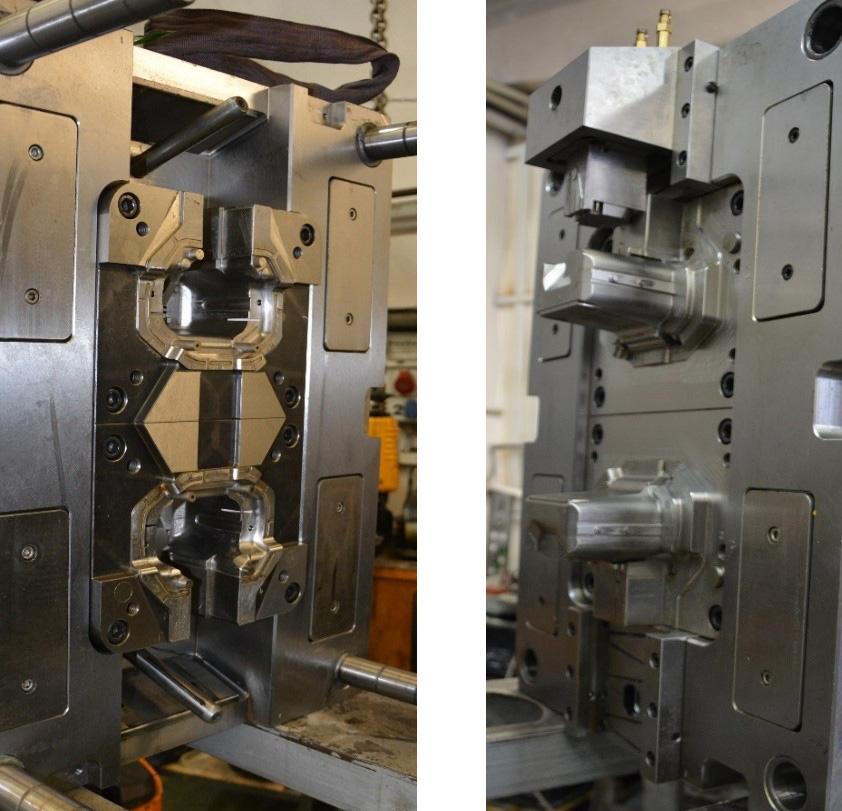
Nejdůležitější ze základních parametrů, které bylo třeba na počátku měření správně nastavit, jsou emisivita a zdánlivá odražená teplota. Pro co nejpřesnější výsledky byla emisivita zjištěna experimentálně – s pomocí kontaktního teploměru byla změřena teplota a experimentálním nastavováním emisivity v termokameře byla nalezena shoda mezi teplotou naměřenou termokamerou (měřená oblast cca 1 cm2) a teplotou naměřenou kontaktním teploměrem.
Z důvodu přítomnosti leštěných částí vstřikovacích forem, které velmi dobře odráží teplotu všech okolních tepelných zdrojů, a také s ohledem na omezený snímací prostor, bylo použito šikmé snímání. Tímto způsobem byly minimalizovány dopady odrazů na zdánlivou odraženou teplotu bez vkládání stínící desky.
Emisivita byla experimentálně stanovena na hodnotu ε = 0,96 a zdánlivá odražená teplota na 30°C. Fotografie formy je zobrazena na Obr. 2.
Použití a vyhodnocení termografické diagnostiky
Pozorovaný díl o velikosti obdélníkové základny cca 125 x 85 mm a hloubce cca 90 mm – byl zaformován do dvojnásobné formy. Způsob zaformování a temperace pomocí fontán s přepážkou je zřejmý z následujícího obrázku (Obr. 3). Tvarové dutiny jsou plněny polymerní taveninou pomocí horkého rozvodu, horká tryska ústí přímo do horní stěny výstřiku. Celková doba výrobního cyklu je 49 s při teplotě formy 100 °C.
Po správném nastavení bylo provedeno několik výrobních cyklů s cílem dostat formu na provozní teplotu – první díl, který byl vyhodnocen jako dobrý (vše bylo správně vyplněno), se podařilo získat po 15 minutách výroby.
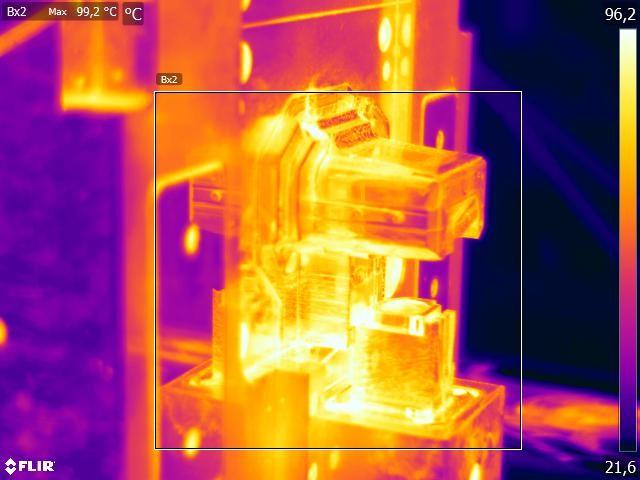
Obr. 4 Teplotní pole spodního dílu pohyblivé části po natemperování na 100°C
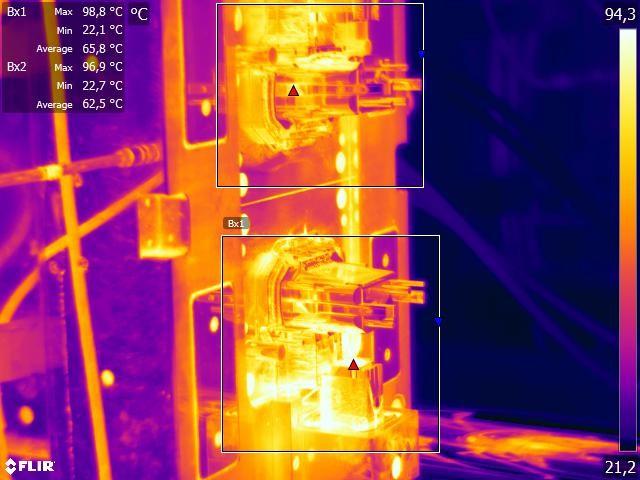
Obr. 5 Teplotní pole spodního dílu pohyblivé části formy u 1. cyklu
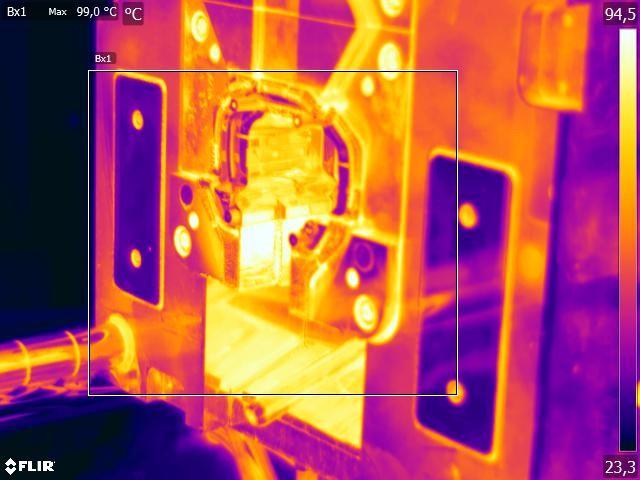
Obr. 6 Teplotní pole spodního dílu pevné části formy u 1. cyklu
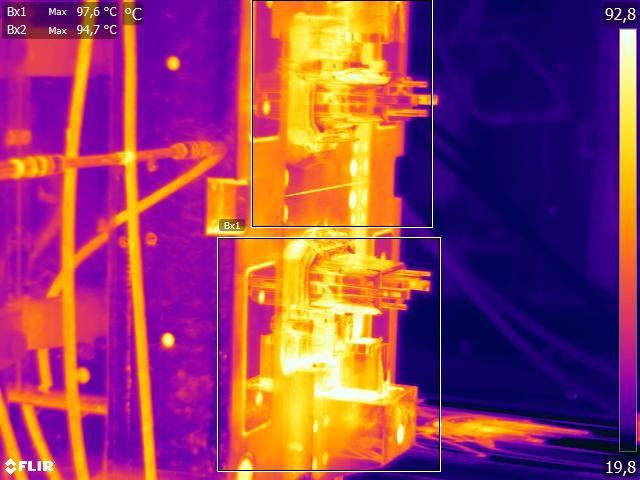
Obr. 7 Teplotní pole spodního dílu pohyblivé části formy u 5. cyklu
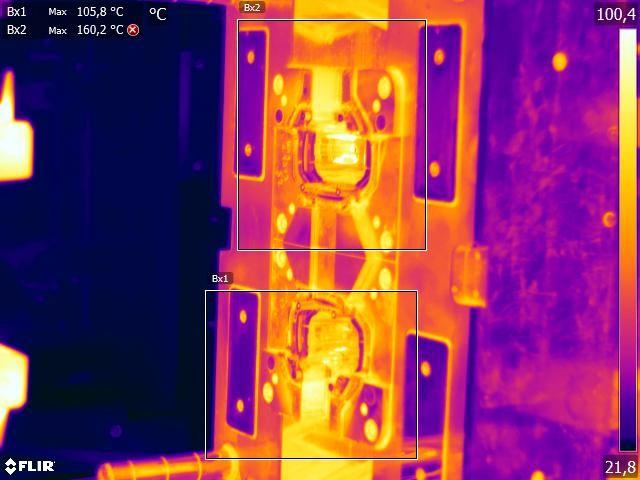
Obr. 8 Teplotní pole spodního dílu pevné části formy u 5. cyklu
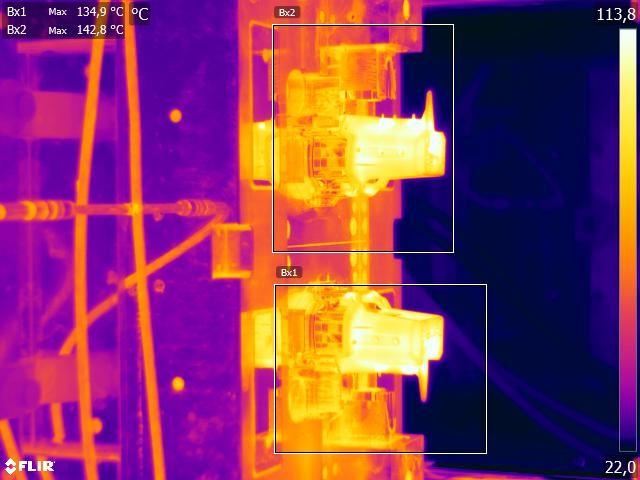
Obr. 9 Teplotní pole spodního dílu pohyblivé části formy u 20. cyklu (ještě s výlisky)
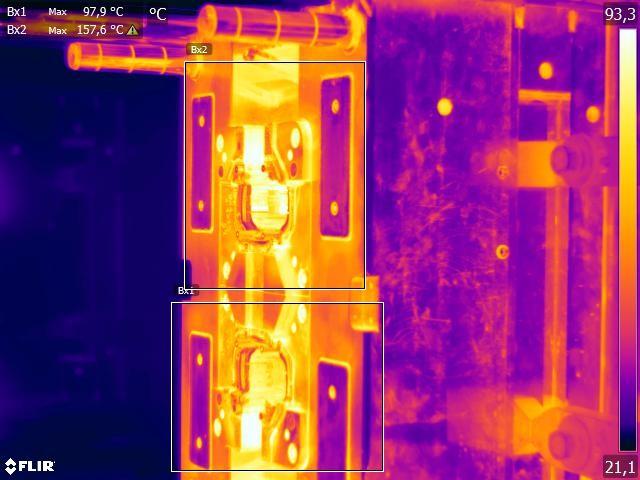
Obr. 10 Teplotní pole spodního dílu pevné části formy u 20. cyklu
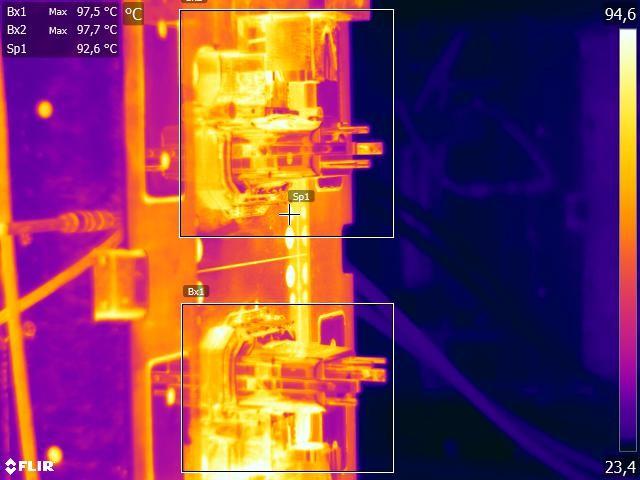
Obr. 11 Teplotní pole spodního dílu pohyblivé části formy u 40. cyklu
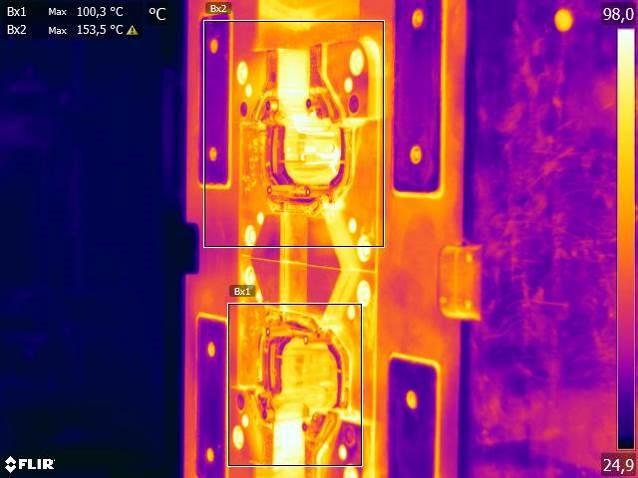
Obr. 12 Teplotní pole spodního dílu pevné části formy u 40. cyklu
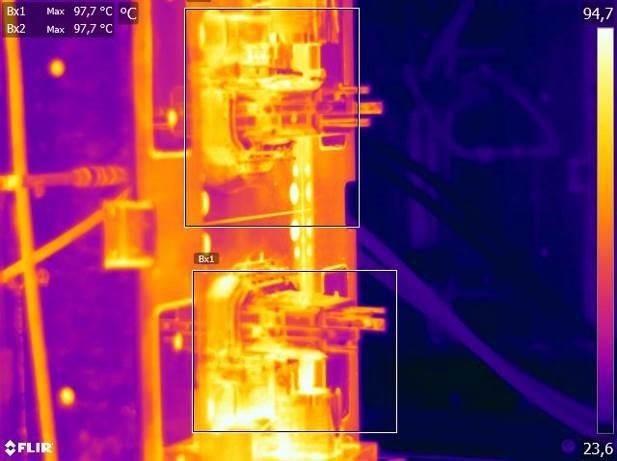
Obr. 13 Teplotní pole spodního dílu pohyblivé části formy u 150. cyklu
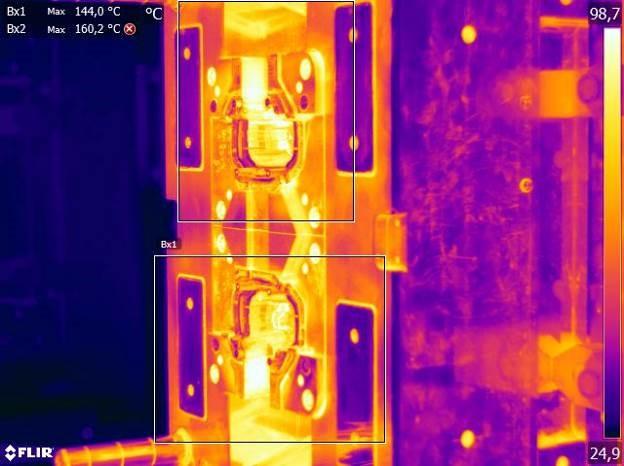
Obr. 14 Teplotní pole spodního dílu pevné části formy u 150. cyklu

Schéma chlazení ve formě
V průběhu tohoto pozorování byl diagnostikován hlavní problém ve špatném chlazení v pevné části formy, kde u horního dílu docházelo k výraznému přehřívání – teplota se pohybovala v rozmezí cca 150–160°C.
S ohledem na to, že u spodního dílu je teplota udržována kolem 100°C a temperační a hladící kanály jsou u obou dílů vedeny symetricky, muselo dojít ke snížení průtoků, či ucpání jednotlivých kanálů. Pro zjištění stability procesu došlo nakonec ještě k nasnímání dílů po 150. cyklu.
Následně se ukázalo, že pohyblivá část formy je ustálená na asi 97–98 °C, zatímco pevná část formy – spodní díl je na teplotě 140°C a horní díl na teplotě 160°C. Toto zjištění vysvětluje, proč problémy s deformací vykazují pouze některé díly, a to ty, které jsou vyrobené v horní části formy a mají jiné deformace díky odlišnému tepelnému poli, které je v ustáleném stavu asi o 20 – 30 °C vyšší, než u spodní části formy.
Závěr
Teplotní vývoj dílů formy v čase ukazuje na důvodný předpoklad toho, že teploty obou tvarových dutin se v čase vyrovnají, což lze považovat za závadu. Pravděpodobným vysvětlením této vady, která se bohužel nutně musí odrazit na kvalitě výsledných výstřiků, je tvarové řešení výstřiků – posuvná čelist a nerovnoměrný rozestup mezi fontánami, přičemž odvod tepla z horní dutiny formy je z určité příčiny omezen – například mohlo dojít k nepřesné montáži fontán, k posunu přepážky ve fontáně, k místnímu zanesení atd.
V přehřátých místech díky zvýšené teplotě dochází k většímu výrobnímu smrštění, než mají okolní tvary, a tedy i k možnosti lokální deformace; tato místa také prodlužují potřebnou dobu chlazení výstřiku v tvarové dutině formy a tím prodlužují i dobu výrobního cyklu.
Z uvedeného příkladu je zřejmý přínos termografické diagnostiky, jako rychlého nástroje sledování stability výrobního procesu. V kombinaci se simulacemi tak lze predikovat problémová místa, kde bude docházet k deformacím. Automatické sledování a vyhodnocování stability výroby termokamerou je přístup, které dokáže odhalit problém při jeho vzniku, nikoliv až při destrukci formy, což zabraňuje nemalým nákladům spojeným s opravami a náhradami vadných výlisků.
Reference:
HERMAN, Aleš a Lubomír ZEMAN. Využití termografické diagnostiky k hodnocení procesů vstřikování kompozitního dílu. Vše o průmyslu [online]. Praha: TRADEMEDIA INTERNATIONAL, 2018, Dostupné z: https://www.vseoprumyslu.cz/udrzba-a-diagnostika/termodiagnostika/vyuziti-termograficke-diagnostiky-k-hodnoceni-procesu-vstrikovani-kompozitniho-dilu.html